Automotive LEDs are one of the LED applications that have not only achieved considerable market size in recent years but are still growing rapidly. In 2016, the trend of global lamp conversion from traditional bulb light source to LED light source continued to accelerate, and more mature markets gradually introduced high-specificity LED light sources.
Nichia, one of the suppliers of automotive lighting LED beading, pointed out that in 2016, the vehicle application has achieved a 20% growth. Looking forward to 2017, it is particularly optimistic about automotive LEDs with high technical requirements, especially with light distribution adjustment. The LED or laser LED of the adaptive lamp system, or the LEDs for the use of the running lights that have recently been gradually grabbed, Japan and Japan will be betting on more technical and equipment resources to ensure the market share of the Japanese market in the automotive market. rate.
At present, in the automotive lighting supply chain in mainland China, from devices, modules, to lights, joint ventures and foreign-funded manufacturers all occupy a large market share, mainland Chinese manufacturers can not compete with it.
In the LED lamp industry chain, from the point of view of the lamp, the domestic car lamp pre-installation market is almost occupied by companies outside mainland China such as Philips, Osram, Nichia, and Jingdian (shared in Dominant).
The huge market potential is the basic judgment of more and more enterprises entering the automotive LED market. At the same time, import substitution is also a huge opportunity for domestic packaging companies. From the past aftermarket, the market has penetrated into the market, and it has become the key strategic layout of domestic LED lighting companies. At the same time, the huge potential demand of the market is also one of the main factors for the company to speed up the layout.
In 2015, the global automotive lighting market totaled approximately US$22.7 billion, and the global market is expected to reach US$27.7 billion by 2021. The market concentration is high, and the total market share of the top five companies is about 73.3%.
China's headlight market has a large room for growth. With the increase in the sales volume of passenger cars, especially new energy vehicles, and the increase in the penetration rate of LED lamps, the market share of domestically produced lamps and supporting LED lamp bead manufacturers under the trend of domestic parts replacing imports. It is expected to improve rapidly.
The latest data of the High-tech Research Institute LED Research Institute (GGII) predicts that the industry market scale will grow steadily in the next few years. It is estimated that by 2020, the LED lighting market in China will reach 57.143 billion yuan, compared with 2016. It increased by 14.867 billion yuan, an increase of 35.17%.
At present, the application of automotive lighting LEDs in automotive interior lighting, taillights, daytime running lights, etc. is very mature. The unit price and gross profit of the lamp products are small lamps, rear combination lamps and headlights. The penetration of LED headlights is still very low, and it is gradually occupying the mid-to-high-end headlight market and infiltrating into the 100,000-200,000 class. It is expected to usher in rapid growth in the future.
At the same time, due to the high added value of LEDs, instead of traditional halogen lamps and xenon lamps, it can bring higher product gross profit levels. AFS and ADB headlamp technologies have been applied to related high-end models, and the future intelligent lights will be Trend.
The huge space for the automotive LED lighting market is attracting more and more companies to participate in it, and companies that have already taken the lead in the market are also expanding their advantages. This is evident from the investment and mergers and acquisitions in the automotive lighting field in the past six months.
01, Hongli Zhihui
On May 2, Hongli Zhihui announced that the company had signed the “Intention to Purchase Equity†with Danyang Xinchen Auto Lamp Factory and Guo Zhiqiang, and planned to invest RMB 230 million to acquire a 51% stake in Danyang Yishan Auto Lamp Equipment Manufacturing Co., Ltd. Through the acquisition of equity interests in companies such as Yishan Auto Lamp and Guangzhou Fo Da Signal Equipment, the company tried to cut into the domestic vehicle lighting supply market and strengthen the layout of LED auto lighting in the domestic vehicle supply system.
Yishen car lights have passed the ISO/TS16949:2002 quality system certification, and the domestic market products have passed the national 3C compulsory certification. The company is now supporting the OEMs and global sourcing companies such as Geely Group, Korea MOBIS, Dongfeng Second Automobile, Great Wall Motor, SAIC Iveco (Hongyan), SAIC Iveco (Nanqi), Fiat, BAIC Group, Zhongxing Automobile, Zhongtai Automobile, etc. It has also expanded foreign trade such as Italy, South Korea, Malaysia and Iran. Yishan car lights promised a non-net profit of 3000/4500/6000/83 million yuan for 2017-2020.
The company is actively building the dual-main business format of “LED+Car Networkingâ€. The hardware of the vehicle networking industry is currently invested in Dina Technology, Hongchuang Power, Hezhong Automobile, etc. The wholly-owned acquisition of the software service has been reviewed by the Securities and Futures Commission. by.
02, Snow Wright
On the evening of June 19, Shellett issued a notice showing that Daewoo Intelligent Manufacturing Industry Fund Partnership (Limited Partnership) was jointly established by Snow Wright and Shenzhen Qianhai Daewoo Capital Management Co., Ltd., and Zhejiang Jiali (Lishui) Industrial Co., Ltd. The company signed the "share subscription contract".
Among them, Jiali shares introduced new investors by issuing stocks, and plans to issue stocks with no more than 13 million shares. Daewoo Intelligent Manufacturing Industry Fund has subscribed for 4.4 million shares of Jiali Shares with a capital contribution of RMB 29.92 million, and the price per share is RMB 6.8. As of the disclosure date of the announcement, Daewoo Intelligent Manufacturing Industry Fund has paid all the share subscription fees.
According to the data, Snow Wright was founded in 1992. It is a representative listed company in the field of electric light source industry in China. The core products developed are energy-saving lamps, HID car xenon headlights, ceramic metal halide lamps, ultraviolet germicidal lamps and other special light sources. Supporting lamps, etc.
Founded on December 25, 2006, Jiali is mainly engaged in the design, research and development, manufacturing and sales of automotive and motorcycle lighting products. It is one of the backbone enterprises in the design and manufacture of domestic vehicle lighting. In September 2015, Jiali shares were officially listed on the New Third Board. In the first half of last year, Jiali shares realized operating income of 390 million yuan, a year-on-year increase of 53.75%; net profit of 24.483 million yuan, an increase of 827.88%.
03, Marelli
On June 20th, the new auto lighting system factory of the world's top 500 companies, the Marelli Group, was put into operation in Changchun Economic Development Zone. The total investment of the Marelli high-end auto lamp project is 1 billion yuan, with an estimated annual output value of more than 2 billion yuan.
Marelli's high-end car lamp project, jointly funded by Italy Marelli Group and Changchun Fudi Equipment Technology Development Co., Ltd., covers an area of ​​30,000 square meters, of which 17,000 square meters are used to produce LED headlights and taillights. 1 million and 500,000, the annual output value can reach 2 billion yuan after reaching production.
According to reports, Marelli's new Changchun plant will produce LED high-end automotive lights that will be launched simultaneously with Europe, and will be supplied to FAW-Volkswagen, BMW Brilliance, Mercedes-Benz, Volvo and other automakers. It is expected to be Japan, South Korea and other countries in the future. The automobile company carries out supporting production.
The Marelli Group is an Italian company that integrates the design, development, production and system of automotive components. It has established 86 plants in 19 countries around the world. The new plant of Changchun Marelli Automobile Lighting System is the ninth factory established in China. The Marelli Group is part of the world's top 500 Italian Fiat Group and is a world-famous auto parts manufacturer. Most of the power systems it produces are provided by well-known top automakers such as Ferrari, Audi, BMW, Mercedes-Benz and Rolls-Royce.
04, Ruifeng Optoelectronics
On the evening of June 26, Ruifeng Optoelectronics announced that the company intends to increase the capital of the holding subsidiary Changzhou Lirui Photoelectric Co., Ltd. (hereinafter referred to as “Li Rui Optoelectronicsâ€) by 20.49 million yuan. After the capital increase, the registered capital of Lirui Optoelectronics is 30 million yuan. Ruifeng Photoelectricity accounts for 70%.
According to the company, the purpose of this foreign investment is: based on the analysis of the automotive industry and automotive LED prospects, combined with the company's own technological advantages and market accumulation in the industry, the company wants to increase investment in the automotive electronics market to achieve LED-related The extension of the industry, the company plans to increase the investment of 20.49 million yuan for Larry Optoelectronics for the R&D and manufacturing of automotive LED modules, and accelerate the company's overall layout in the field of LED applications.
The data shows that Lirui Optoelectronics' 2016 annual revenue is 11.0965 million yuan and net profit is 174,800 yuan. In the first quarter of 2017, revenue was 3.114 million yuan and net profit was 49,000 yuan.
05, Hella Group
Recently, Hella Group, an expert in automotive lighting and electronics, will set up a new location in Ljubljana, not far from its Slovenian headquarters. Integrate the technologies of the Group's body light business unit and rename its product group as a small body light. The new site plans to employ approximately 160 people.
At the opening ceremony of the small body lighting department, Markus Bannert, general manager of the global automotive lighting business unit said: "After the integration of technical capabilities, we will be able to better play the growth potential of Hella in the field of exterior lighting." The Light Business Division covers fog lighting, daytime and front combination lights, rear fog lights, high brake lights and auxiliary turn signals, rear signal lights and license plate lights for automotive exterior lighting.
John Kuijpers, head of the interior lighting and body light product center, said: "The new lighting components are better able to meet new trends and show the appearance of the vehicle with appropriate lighting." For example, we can light up Intake grille or door frame. Or, when the driver enters the car, the welcome light is projected onto the ground to provide an extremely unique experience. Since then, the new name of the body light will more effectively reflect the breadth and importance of the Hella product line.
06, Osram
According to Reuters, Ingo Bank, head of finance at Osram, Germany, revealed in an interview with the German media "Securities" that Osram is seeking mergers and acquisitions, with a total acquisition of 500 million euros ($530 million), although there are no specific transactions. plan.
Ingo Bank said that OSRAM hopes to strengthen its electronics and software sectors under the automotive lighting sector and is looking for acquisition targets or partners. Osram has a large amount of funds available after the sale of the lighting department LEDvance, which brought the company a total revenue of about 500 million euros.
In the first quarter of fiscal 2017, the performance report showed that OSRAM was affected by the adjusted portfolio and currency, and its revenue in the fourth quarter of 2016 increased by nearly 8% compared with the same period of the previous year. The LED component business (optoelectronic semiconductor or OS) achieved growth, with revenue growth of 15% over the same period last year, with the growth of the automotive and infrared businesses particularly strong.
Earlier, OSRAM said that by 2020, the company's optical semiconductor factory will increase its manpower by about 50%, mainly responsible for manufacturing and R&D to balance the demand for LED components and infrared rays for assisted driving systems. The company also plans to invest 10 million euros ($10.64 million) in the production of LED components in the new plant in Kulimia.
On October 4, 2016, OSRAM successfully completed the acquisition of Novità Technologies. Novità Technologies is a well-known manufacturer of automotive LED modules in the United States. Its products are mainly used as taillights, fog lights and daytime running lights. Through this acquisition, OSRAM will further expand its position in the US automotive LED market and enrich the product portfolio of LED modules in automotive projects.
07, Japan Panasonic
In December last year, according to the report of the Nihon Keizai Shimbun, Japan’s Matsushita has decided to acquire the Austrian automotive lighting manufacturer ZKW Group to enter this business area. The two companies have now initiated final negotiations, and the estimated acquisition amount will reach 100 billion yen.
ZKW's main products are energy-saving, long-lighting and high-brightness automotive light-emitting diode (LED) headlights. It has production and research bases in Europe, America, China and India. Founded in 1938, ZKW Group's main customers include large-scale European and American automakers such as General Motors. Sales in 2016 are expected to reach approximately 900 million euros and the global workforce is approximately 7,500.
In the era of automatic driving, the lights will become important key components for safety. Since the vehicle has to travel, it is necessary to predict the direction of advancement and change the direction of illumination, and the development of technology for adjusting the brightness is evolving. Because Panasonic has extensive experience in sensors and other fields, the acquisition of the ZKW Group will help develop new types of lights with enhanced identification to catch up with leading companies in the industry.
08, An Rui Optoelectronics
Wuhu Anrui Optoelectronics is the strategic focus of Sanan Optoelectronics' development of automotive lighting business. The investment of the first phase of the project is nearly RMB 200 million. The revenues in 2015 and 2016 are 256 million yuan and 510 million yuan respectively.
The second phase of the intelligent car lamp project is under construction, with an investment of 968 million yuan, which is an important part of the company's vertical integration of the entire industry chain, which will promote the rapid increase of the company's LED products in the automotive lighting market.
Wuhu Anrui Optoelectronics Co., Ltd. was established in June 2010 by Sanan Optoelectronics and Chery Automobile. Its main business is divided into two parts: automotive lighting, LED packaging and application. Previously, the planned production capacity was to reach the annual production capacity of 1 million automobile complete lamps and 200KK full-color LED packaging products in 2016.
Anrui's production strength in automotive vehicle lighting and full-color LED packaging products has made it a professional domestic automotive lighting manufacturer. In addition, Anrui has a design and manufacturing team with more than 10 years of experience in headlights and light sources. It has the strength to meet the differentiated needs of the lamp market and meet the CCC, ECE, SAE and other standards.

Metal Core PCB, MCPCB Manufacturing Service
Overview of Metal Core PCB
Metal Core PCB, The printed circuit boards good thermal management solutions.
Metal core PCB (MCPCB), also known as heat sensitive PCB, insulated metal substrates (IMS PCB), Metal PCB, Metal Base PCB, Metal Backed PCB, Metal Clad PCB, etc., are designed to provide good thermal management, using metal substrates as circuit boards for radiator parts of circuit boards. These metal materials have high thermal conductivity. Aluminum is the most economical choice because it has good heat conduction and heat dissipation capacity and is cheaper than copper and steel. However, in order to adapt to different use scenarios, people choose different materials. Base metals in MCPCB are used as substitutes for FR4 or CEM3 boards. They radiate heat from key panel components to less important areas, such as metal radiator backings or metal cores. With the latest development of high power LED, the demand for MCPCB has exploded.
MCPCB is mostly single-sided IMS, metal core PCB manufacturer can also produce double-sided MCPCB, sometimes multi-layer IMS PCB and metal core PCB Prototype according to need. They have very advanced and perfect metal core PCB manufacturing process. Whichever MCPCB is chosen, the heat dissipation capability should be taken into account when choosing the thickness of base material and copper. The thermal conductivity is expressed in W/mK. The value of standard aluminium sheet is 1.0 W/mK, but other options may be 2.0, 3.0 or even 5.0 W/mK.
Most MCPCB surface treatments use HASL LF. Without fine spacing elements and BGA, HASL LF may be the most suitable finish for power LED components. However, nothing prevents us from proposing all other surface treatments; OSP, ENIG, Chem Tin or Silver for IMS applications.
Metal Core PCB for LEDs
Thermal Management PCBs are necessary for high power LED applications due to the amount of heat that LEDs generate. The bare board is the real estate that sustains electronic components such as LEDs. PCBs containing a metal core dissipate heat in LED applications. Furthermore, the MCPCB provides a much lower thermal resistance for light emitting diode applications.
The LED on the metal core printed circuit board (MCPCB) is designed to provide high power output in compact packaging. Each LED package contains an LED welded to MCPCB. These LEDs are very suitable for OEM or custom applications; therefore, they should not be used for home lighting.
Metal Core PCB Design Specifications
Metal Core PCB designers always focus on price and manufacturability. However, you can rest assured that we have experienced engineers who have been engaged in DFM inspection for many years, and provide you with suggestions for choosing the best materials.
Detailed Introduction of Metal Core PCB
Conventional PCB use FR4 epoxy glass-based material on both sides of a board. However, with the growing popularity of light-emitting diode or LED technology, metal core printed circuit board or MCPCB are being deployed to deal with the increased heat LEDs generate.
Today, metal core PCB are finding greater numbers of applications in the automobile industry, traffic light signal technology, in commercial buildings, shopping malls, and even inside homes.
MCPCB use either an aluminum or copper core with the bottom side of the board serving as the heat sink. MCPCB are also used to dissipate heat in intense power-generating analog circuitry.
Metal core PCB are connected through mounting holes and screws through a box build's chassis. In this arrangement, heat is not only dissipated through the metal core, but it is also transmitted to the chassis. Hence, an LED or analog device-populated board has a considerably larger surface finish for the purpose of dissipating that heat.
But here's a word of caution about using MCPCB – actually two things to be cautious about.
- One, you need to know that making an MCPCB is complex and complicated because a metal layer is laminated with FR4, a glass-base material. Therefore, the chemistry for lamination is different during board fabrication. There is a fair possibility that there would be voids underneath the lamination, if it is not bonded properly.
- Two, a fixture to dissipate the heat from the metal core needs to be carefully defined and designed. Both these concerns demand experience.
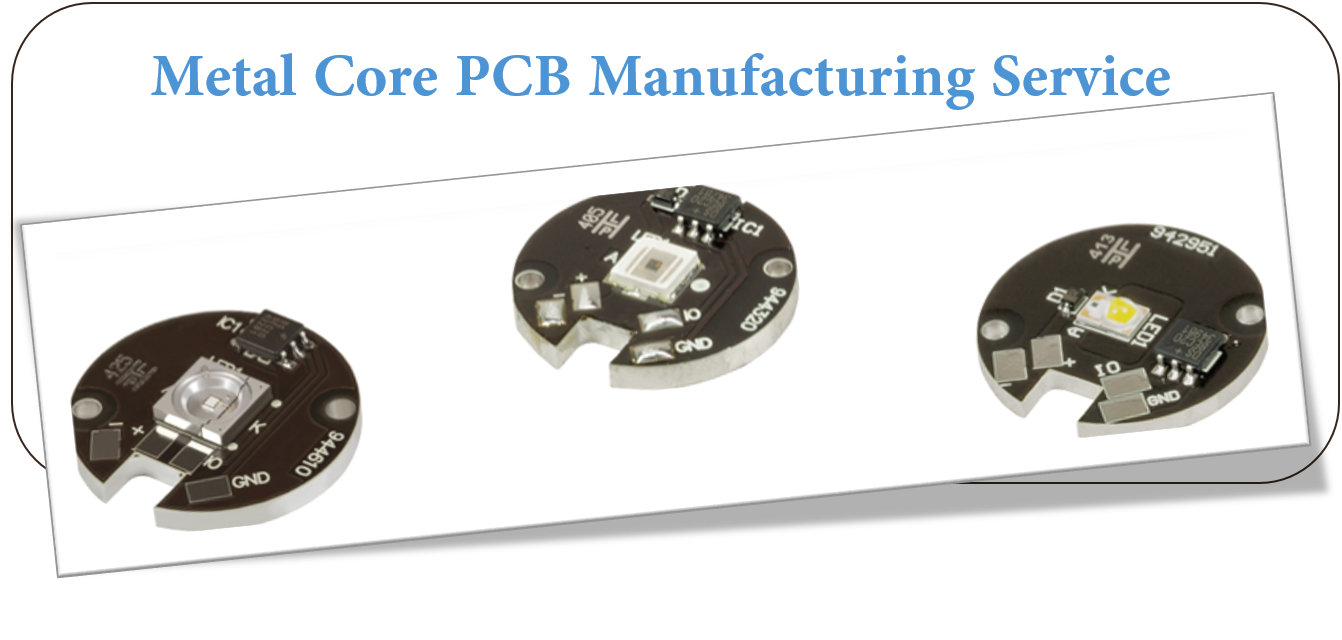
At JHYPCB, we've been doing this for a long time, as one of professional MCPCB/Aluminum PCB manufacturers from ShenZhen, China. We can produce metal core PCB prototype or aluminum PCB prototyping, aluminium PCB board for led, No Quantity Requirements, and can successfully guide you through your next MCPCB project. We have worked with over half a dozen LED manufacturers over ten years and have seen enormous amounts of different applications using MCPCB.
Choose us to provide PCB manufacturing services for you. Contact us immediately.
How Do Metal Core Circuit Boards Differ From FR4 Boards?
The dielectric material`s thermal conductivity is measured in Watts per meter, Kelvin (W/mK.) A 2.0W rating is fairly common; such material is approximately 6x-7x as thermally conductive as FR4. Best practice is to keep the dielectric layer as thin as possible. Doing so creates the shortest possible path from the heat source to the metal backing plate which is many times more thermally conductive than the dielectric material. Most of the materials come in a very limited range of thicknesses anyway, usually between .003" and .006". You won`t have all that much opportunity to specify something thicker that could diminish the effectiveness of the material at performing its thermal transfer function.
The metal backing plate used on the bottom side is the thickest element in the structure. It is available in several different thicknesses but it is best to use one of the three most common (1.0mm, 1.5mm, and 3.2mm) because they are the easiest to purchase without delays. The metal layer adds rigidity, keeps the circuit flat, and adds enough thickness so that the MCPCB can use the same mounting hardware that would be used for any other standard thickness circuit board. The metal plate side of the board does not receive any surface finish or soldermask.
Metal Core PCB Vs. Fr4 PCB Comparison
- Conductivity: FR4 has low thermal conductivity, typically around 0.3W, while MCPCB has higher thermal conductivity, ranging from 1.0W-4.0W, most commonly around 2.0W.
- Plated Through Holes: FR4 PCB typically uses plated through holes. Through hole components possible if required. In MCPCB, plated through holes are not available for 1-layer PCB. All components are surface-mounted.
- Thermal Relief: Thermal relief in FR4 PCB typically involves vias for heat transfer. Longer drill cycle, adds many processes. MCPCB materials provide their own thermal relief. Via drilling, deposition, and plating processes are eliminated.
- Solder Mask: FR4 PCB solder mask is typically dark colors (green, red, blue, black.) Usually applied top and bottom. MCPCB solder mask are almost exclusively white for LED boards. Applied to top only.
- Thickness: FR4 PCB has a wide range of thicknesses available using various material combinations and layer counts. MCPCB thickness variation is limited by available backing plate thicknesses and dielectric sheet thicknesses.
- Machining Process: FR4 PCB uses standard machining practices (drilling, routing, v-scoring, countersink, counterbore) while MCPCB uses the same machining as FR4, except that v-score must use diamond coated saw blades for the added strain from cutting into metal.
Metal Core PCB Material
Metal Core PCB means the core (base) material for PCB is the metal, not the normal FR4/CEM1-3, etc. and currently the most common metal used for MCPCB manufacturer are Aluminum, Copper and steel alloy. Aluminum has good heat transferring and dissipation ability, but yet relatively cheaper; copper has even better performance but relatively more expensive, and steel can be divided into normal steel and stainless steel. It more rigid than both aluminum and copper, but thermal conductivity is lower than them too. People will choose their own base/core material according to their different application.
1. Aluminum PCB
Aluminum PCB , also, it is called Aluminium PCB, metal core PCB, MCPCB, IMS(Insulated metal substracte).
Aluminum PCB have 3 parts:
- Circuit Layer (Copper Layer)
- Dielectric Layer(Insulated Layer)
- Substrate Layer(Metal layer)
Aluminum Clad PCB
Available as 1 layer Non-Plated Through Hole (single sided), And 2+ layer Plated through Hole. Ideal application for LED lighting, power supply solutions. Aluminium Clad Benefits Include:
- Lower operating temperature.
- Reduce printed circuit board size.
- Increase power density.
- Extend the life of dies.
- Reduce the number of interconnects.
- Improve product thermal and mechanical performance.
- Combine power and control.
- Improve product durability.
- Enable better use of surface mount technology.
- Expedite heat sinks and other mounting hardware.
- Replace fragile ceramic substrates with greater mechanical durability
About Price:
- Price is based on the requirement of LED PCB
- PCB thickness: 0.6 – 3.0mm, always thickness more ,price higher
- Thermal conductivity: 1.0 – 10 W/m.k , thermal conductivity higher, price higher
- Material factory: Bergquist, Laird ETC, made in US factory that is more expensive than China.
2. Copper Core PCB
Copper core PCB is a copper substrate + Insulated layer + copper
Copper core PCB is a copper substrate + Insulated layer + copper circuits layer PCB, also, it is called copper substrate pcb, copper based pcb, copper clad pcb.
As a MCPCB manufacturer, we made various Copper core PCB for customers, Which used for High Power LED lighter ( 1000W+ ) and power supply.
In LED field, there are 4 types of Copper based Circuit Board.
COB Copper PCB(Chip on Board copper PCB)
Direct thermal path, no dielectric layer under the thermal path pad.
Direct thermal path, no dielectric layer,Aluminum-copper pcb.
3. Iron Based PCB
The iron-based PCB use material for the base is from special steel, silicon steel and ect in stand of FR4 or CEM1 and can dissipate heat away from critical board components and to less crucial areas such as metallic core or the metal heatsink backing.
China PCB manufacturers becomes more and more professional on Iron-Based PCB.
The Iron-based PCB has all the functions as metal materical and the following particular characteristics:
- Vacancy area convenient for further machinery , procuring and fixing of the base ;
- High mechanic strength, good forther machinery suitable for the assembly heaven electronic parts on its surface;
- Silicon-steel is iron magnetic, and can be applied on micro-motors such as on VTR, FDD.
Metal Core PCB Stack up and Thickness
Single Layer Metal Core PCB Stack Up
![]() |
It consists of a single copper conductive layer on top, a metal base plate (e.g. Aluminum) to provide rigidness to the circuit board and a thermal conductive dielectric working as the insulator. |
Double Sided Metal Core Stack Up
![]() |
It has two copper layers and the metal core is between the copper layers. Plated Through Holes (PTH) are used to interconnect the acopper layers so SMT and THT components can be placed on both sides. |
Multilayer Metal Core PCB Stack Up
![]() |
It has more than two conductive layers separated by thermal dielectric. In the bottom of the structure is the metal base. SMT components can only be placed on one side. Not THT components are allowed, but it provides the possibility to make blind and buried vias with internal signal layers and power/ground planes. |
MCPCB copper foil thickness can be 1 - 10 oz.
Benefits of Metal Core PCB Fabrication
Metal Core PCB Fabrication produces a product that transfers heat up to nine times more rapidly than a typical FR4 PCB. The laminates in MCPCB's dissipate heat which ensures that components which generate heat will remain cooler. This leads to a longer operating life as well as maximized performance for such components.
Applications of Metal Core PCB Fabrication
Although LED-based Solid State Light technologies have countless advantages, they inherently produce significant amounts of heat. This makes Metal Core PCB Fabrication helpful for applications like:
LED lights
High-current
LED, Spotlight, high-current PCB
Industrial power equipment
High-power
transistors, transistor arrays, push-pull or totem pole output circuit (to
tem pole), solid-state relay, pulse motor driver, the engine Computing
amplifiers (Operational amplifier for serro-motor), pole-changing device
(Inverter)
Cars
firing
implement, power regulator, exchange converters, power controllers, variable
optical system
Power
voltage
regulator series, switching regulator, DC-DC converters
Audio
input -
output amplifier, balanced amplifier, pre-shield amplifier, audio amplifier,
power amplifier
OA
Printer
driver, large electronic display substrate, thermal print head
Audio
input -
output amplifier, balanced amplifier, pre-shield amplifier, audio amplifier,
power amplifier
Others
Semiconductor
thermal insulation board, IC arrays, resistor arrays, Ics carrier chip, heat
sink, solar cell substrates, semiconductor refrigeration device
Other applications that are ideal for MCPCB integration are solar panels and motion control applications. We can also combine metal core with our HDI PCB technology. We also offer other advanced circuit technology including Flexible PCB Rigid PCB , and Rigid Flex PCB.
Additional information
Metal Core PCB manufacturing process
Metal Core PCB Manufacturing Capability
LED Lighting and MCPCB (Metal Core PCB)
Understanding the Importance of Metal Core PCBs
METAL CORE PCB VS STANDARD CIRCUIT BOARDS
Metal Core PCB is the best source for the heat transformation
Are Metal Core PCBs the Solution to Your Thermal Management Challenges?
Printable Circuit Boards,Metal Core PCB,Metal Core Led PCB,Metal Core PCB Prototype
JingHongYi PCB (HK) Co., Limited , https://www.pcbjhy.com